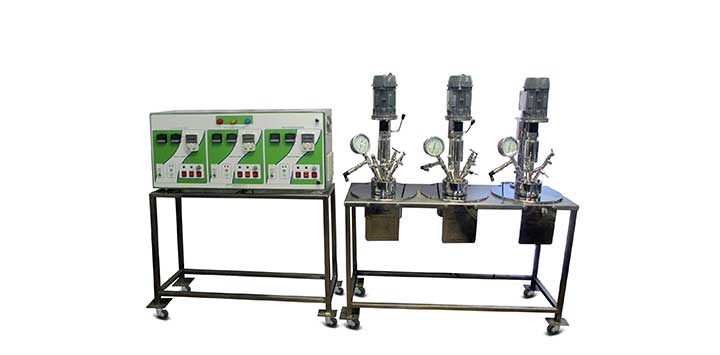
Description
Nano-Mag Technologies is a manufacturer of Continuous Stirred Tank Reactor (CSTR, or stirred tank reactor STR) with design pressure range from full vacuum to 350 bar (5000 psi) and temperature range up to 600°C. In a CSTR, one or more reactants are introduced into a reactor equipped with an impeller (stirrer) and the products are removed continuously. The impeller stirs the reagents vigorously to ensure good mixing so that there is a uniform composition throughout. We take care of flow rate & agitation process, material and energy balance for batch CSTR.
When high conversions of reactants are needed, several CSTRs in series i.e. cascades of CSTR can be used. Equally good results can be obtained by dividing a single vessel into compartments while minimizing back-mixing and short-circuiting. If severe heat-transfer requirements are imposed, heating or cooling zones can be incorporated within or external to the CSTR. Continuous stirred-tank reactors or Back Mix Flow Reactors (BMR) are most commonly used for performing various iso-thermic, endothermic and exothermic reactions in industrial processing, primarily in homogeneous liquid-phase flow reactions, where constant agitation is required. CSTR i.e. Mixed Flow Reactor (MFR) is also used in the pharmaceutical industry as a loop reactor. Also reactions between gas-liquid, liquid-liquid, fluid-solid phases are often tested in CSTR.
We offer magnetically coupled, seal-less agitator with backmix reactor. We also offer a control panel from simple manual controls to advanced PC-based SCADA system. We manufacture tailor-made Tank reactors as per the customer’s requirement. Along with the reactors we also can supply feed tanks as per your requirements. Contact our sales team for your requirement of Continuous Stirred Tank Reactor.
Request For Proposal
Other Products
Advantages & Benefits
- Back Mixing: Complete back -mixing resulting in a minimization of the substrate concentration, and a maximization of the product concentration
- High Yield: Optimum residence time ensures high yields at minimum cost
- Good Temperature Control: Easy to maintain the reactor at isothermal conditions for high heat of reaction
- Automatic Control: Computer controlled scada system with data logging and automatic control is available as option
- Touch Control: Optional integrated operator interface touch panel
- Complete Safety: Safety assemblies provided on vessel protects vessel and operator from the hazards of unexpected high internal pressure
Features:
- Sizes from 50ml to 100 liters
- Pressure range up to 350 bar
- Temperature range up to 600°C
- Different material of constructions like SS 316, SS 316L, Hastelloy C, Zirconium, Inconel, Monel, Titanium etc.
- Conforming to international standards CE, PED, ASME, ATEX etc.
Specifications | 1000 Series (Lab Scale) |
2000 Series (Lab Scale) |
3000 Series (Kilo Lab Scale) |
||||||||||
---|---|---|---|---|---|---|---|---|---|---|---|---|---|
Autoclave Model Number | NMCR 1050 | NMCR 1100 | NMCR 1400 | NMCR 1750 | NMCR 2001 | NMCR 2002 | NMCR 2005 | NMCR 2010 | NMCR 2020 | NMCR 2025 | NMCR 3050 | NMCR 3100 | |
Total Volume | 50 ml | 100 ml | 400 ml | 750 ml | 1000 ml | 2 litres | 5 litres | 10 litres | 20 litres | 25 litres | 50 litres | 100 litres | |
Operating Volume | Maximum | 35 ml | 50 ml | 200 ml | 400 ml | 600 ml | 1.2 litres | 3.5 litres | 7 litres | 15 litres | 19 litres | 38 litres | 75 litres |
Minimum | 18 ml | 25 ml | 80 ml | 80 ml | 80 ml | 150 ml | 500 ml | 1 litre | 2 litres | 2 litres | 4.5 litres | 8.5 litres | |
ID | 50 | 50 | 90 | 90 | 90 | 114 | 162 | 205 | 276 | 276 | 320 | 425 | |
L/D Ratio | 1 | 1.4 | 1 | 1.39 | 1.94 | 1.96 | 1.54 | 1.3 | 1.36 | 1.59 | 1.78 | 1.63 | |
Maximum Head Openings | 5 | 5 | 4 | 4 | 4 | 4 | 4 | 4 | 4 | 5 | 5 | 5 | |
Motor Rating (HP) | 0.25 | 0.5 | 1 | 1.5 | |||||||||
Motor Type | Standard | Flame proof AC motor for Group IIA & IIB gases | |||||||||||
Optional | Flame proof AC motor for Group IIC gases | ||||||||||||
ATEX (Explosion Proof) | |||||||||||||
Vessel Material | Standard | SS 316 | |||||||||||
Optional | SS 316L, Hastelloy C-276, Hastelloy C-22, Nickel-200, Monel-400, Inconel-600, Inconel-625, Titanium, Zirconium etc. | ||||||||||||
Design Pressure | Standard | 100 bar | 50 bar | ||||||||||
Optional | 200 bar, 350 bar | 100 bar | |||||||||||
Design Temperature | Standard | 250°C | |||||||||||
Optional | 350°C, 500°C (600°C for Inconel) | 350°C | |||||||||||
Heating System | Standard | Electric Ceramic Band Heater with Flameproof Group II A/B Junction Box & Ceramic Wool insulation & SS 304 Cladding | |||||||||||
Optional | Aluminum Cast heater with Flameproof Group II A/B Junction Box & Insulation | ||||||||||||
Aluminum Cast heater with Flameproof Group II C Junction Box & Insulation | |||||||||||||
Insulation & Cladding | |||||||||||||
SS Jacket | NA | ||||||||||||
Internal Fittings | Standard | Single Tube in Tube out cooling coil (upto 100 ml), Helical cooling coil (from 400 ml), Thermowell, Dip tube | |||||||||||
Optional | Dip tube with Filter | ||||||||||||
Fittings on Vessel | Standard | Pressure Gauge, Safety Rupture Disc, Vent Valve, Gas Inlet Valve & Sampling Valve with Dip tube, | |||||||||||
Temperature sensor (Flp/Exp) | |||||||||||||
Optional | Pressure Relief Valve, Flush Bottom Valve, Ball Valve with charging funnel, Pressure Transmitter (Flp/Exp) | ||||||||||||
Agitator | Standard | Hollow shaft with High mass transfer area impeller for gas recirculation | |||||||||||
Optional | 6 Blade Disc Turbine, 4 Blade 45° PBT, Anchor, Helix | ||||||||||||
Agitator Sealing | Nano-Mag make Zero Leakage Magnetic Drive Coupling | ||||||||||||
Gasket | Standard | PTFE | 'O' Ring | ||||||||||
Optional | Spiral Wound Metallic Gasket | ||||||||||||
Non Asbestos (High Temperature) | |||||||||||||
Electrical Supply | Volts AC | 1Ø, 220 ± 10% | 3Ø, 415 ± 10% | ||||||||||
3Ø, 415 ± 10% for Multiple Autoclaves | |||||||||||||
3Ø, 415 ± 10% Flameproof with Autocooling | |||||||||||||
Frequency | 50 Hz (60 Hz Optional) | ||||||||||||
Control Panel | Standard | Non Flame proof SS Control panel | |||||||||||
Optional | Flameproof Group II-A/B control panel | ||||||||||||
Flameproof Group II-A/B+H₂ service | |||||||||||||
ATEX (Zone 1) | |||||||||||||
Mounting | Standard | Table Top | Trolley | Floor Stand | |||||||||
Optional | Trolley | Table Top | NA |
All Products, Product Specifications and Data are subject to change.
Request For ProposalAuto-cooling System
The system is useful to control temperature overshoots for exothermic reactions. A cooling liquid is continuously circulated through internal cooling coil. Through our efficient Auto-cooling systems, it is easy to achieve fast and effective cooling of the reaction mass. The circulation of cooling liquid through the internal cooling coil will be switched on/off automatically after sensing the temperature of reactor. The system comprises of circulation pump, hose pipes with quick release coupling, SS 304 water tank. We offer Flameproof II-A/B, II-C & Non-Flameproof options as per requirement.
Back Pressure Regulator
Back pressure regulators are designed to provide steady control of inlet or upstream pressure in the autoclave. If the autoclave pressure increases, the regulator opens to vent out additional flow through the device. As the pressure decreases the regulator closes to restrict flow. This automatic adjustment of flow stabilizes the autoclave pressure.
Ball Valve with Funnel
It is used to charge solid/liquid at Atmospheric pressure.
Chain Pulley
Weight of Head and Vessel increases with increase in size of the autoclave. For large reactors above 10 liters, it is difficult to handle heavy vessels and head. For such large autoclave we offer Chain Pulley Block arrangement as an option. With chain pulley block it becomes easy to lift the head or vessel of big autoclaves. We offer Electric (motorized) or Manual chain pulley blocks as per requirements.
Condenser
The condenser is used for condensing the vapors from autoclave. The condensed liquid can be collected in receiver pot or refluxed back in to the autoclave. We offer shell & tube condensers with surface area 0.1m², 0.2m², 0.5m², 1m² and 2m². We also supply custom size condensers with different MOCs like SS 316, SS 316L, Hastelloy C-276, Inconel etc.
Digital Pressure Indicator
It is offered in addition to Analogue pressure gauge which is fitted on the vessel as standard accessory. Digital pressure indication unit comprises pressure transmitter fitted on the autoclave & digital pressure indicator mounted on the control panel with high pressure alarm. We offer Digital Pressure Indicator in different Material of Constructions like SS 316, SS 316L, Hastelloy C-276, Inconel etc. with Flameproof / Non-Flameproof Pressure transmitter.
Flameproof Control Panel
Flame-proof control panels are mostly used in places with high concentration of flammable gases, vapors or dust. Electrical equipment which are installed in such conditions must be designed with flame proof enclosure to ensure it does not initiate an explosion due to arcing contacts or high surface temperature of instrument. We offer Complete Flameproof control panels enclosed in Aluminum casting for hazardous area for Zone-1, Group IIA/IIB or IIC as per the requirement.
Flush Bottom Valve:
Liquids & Slurry is discharged from the bottom of Autoclave / Reactor through Flush Bottom Valve. We offer zero hold-up, high pressure FBV with different materials of construction like SS 316, SS 316L, Hastelloy, Zirconium, Inconel, Monel, Titanium etc.
Gas Pressure Regulator:
These are used for charging different gases like Hydrogen, Nitrogen, Air etc. from the gas cylinder to the autoclave. It ensures a constant outlet pressure range from 1 to 100 bars. It regulates the pressure at the outlet of a cylinder to a set value regardless of the pressure inside cylinder. We offer SS 316 Pressure Regulator with Pressure Gauge, NRV, 4 meter long SS braided hose pipe & quick release coupling.
High pressure gas/liquid charging system:
This system is used to inject liquid/gases under pressure up to 100 bar during the reaction. It comprises of high pressure pot, valves, NRV, pressure gauge, high pressure hoses with quick release coupling. We offer 500ml, 1 Litre, 2 Litres, 5 Litres size High pressure gas/liquid charging system with different MOCs like SS 316, SS 316L, Hastelloy C-276, Inconel etc.
Pressure Relief Valve
PRV is a safety device designed to protect a pressurized vessel or system during an overpressure event. It is necessary for additional safety of the autoclave & acts as a supplement to any safety device. The spring loaded Pressure relief valve releases the excess pressure when pressure inside the reactor increase beyond the specified design pressure or maximum allowable working pressure (MAWP), protecting the vessel & the operator. We offer PRV with different MOCs like SS 316, Hastelloy C-276, Inconel etc.
Receiver pot
Receiver pot is installed at the outlet of the condenser to collect the condensate.
Reflux Condenser
Reflux condenser condenses vapors produced in autoclave and drops the condensate back in to the autoclave. It consists of a water jacketed tube of 0.02 m² heat transfer area, connected directly to the vent of the autoclave. Condensed vapors from the autoclave are refluxed directly into the vessel and uncondensed vapors are released through a needle valve at the top of the condenser. We offer Reflux Condenser in various sizes like 0.01m², 0.02m², 0.05m² with different MOCs like SS 316, SS 316L, Hastelloy C-276, Inconel etc.
SCADA Software
Supervisory Control and Data Acquisition (SCADA) is a software used for remote monitoring and control of the reactor / autoclave system. The process data is presented on a computer screen to operators where they monitor and control the process. We offer operator friendly SCADA based software for monitor and control of all parameters. Computer is usually in client’s scope.